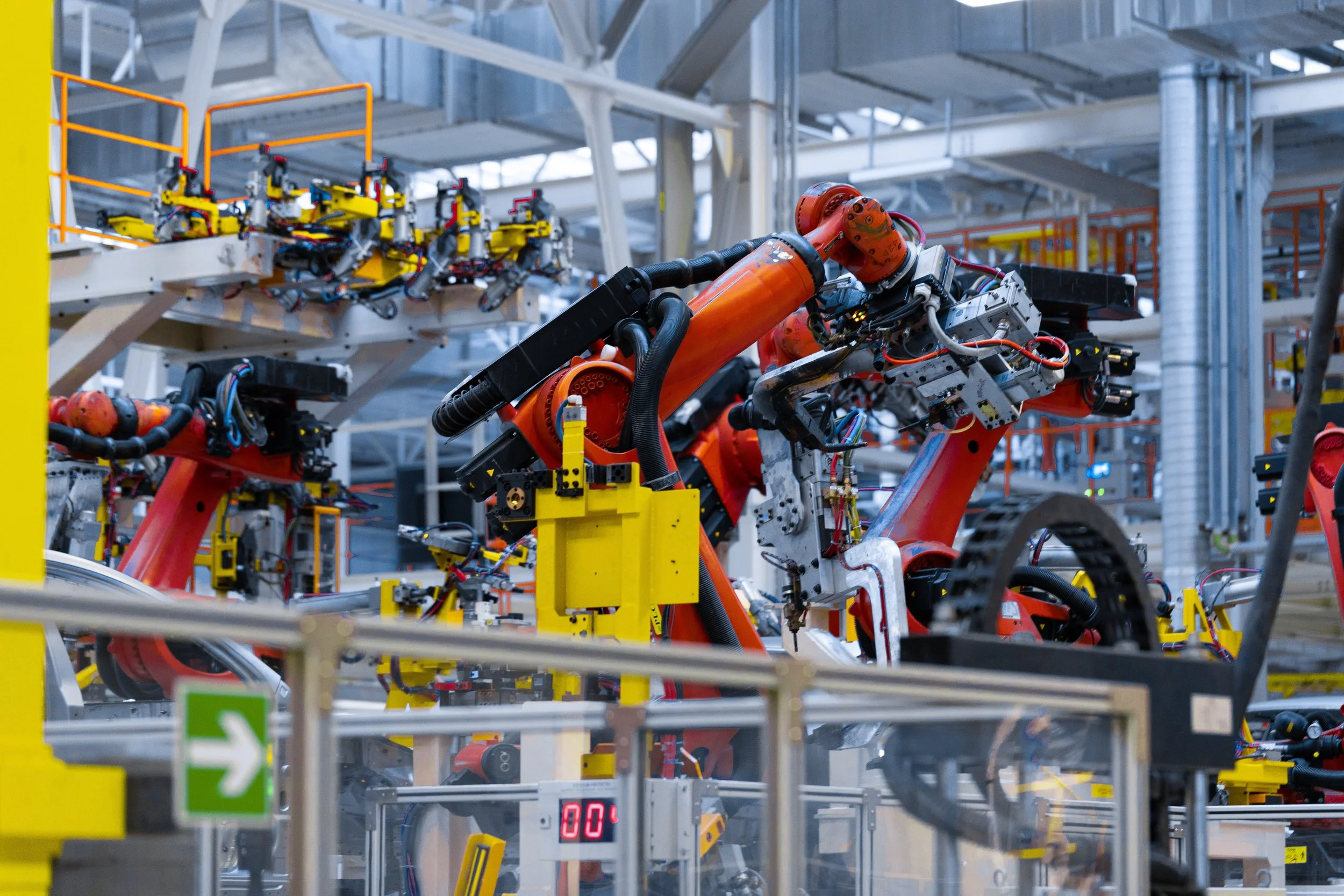
FREQUENTLY ASKED QUESTIONS
-
Primary steel is new steel typically created today in a process that is heavily reliant on burning coal. Steelmakers combine iron ore with coke, a product made from metallurgical-grade coal, in a blast furnace. The iron ore and coke chemically react to produce metallic iron and carbon dioxide. Some of the heat needed for this reaction may also come from coal combustion. This iron is then processed into steel in a basic oxygen furnace. As a result of this process, primary steel accounts for 90% of the global emissions from steelmaking.
Secondary steel is essentially recycled steel. It’s made from melting scrap steel in an electric arc furnace. Secondary steel makes up 10% of the global emissions from steelmaking due to the electricity used to power the electric arc furnaces, because many of these furnaces draw power produced from fossil fuel combustion.
Note: while primary steel chiefly uses iron ore, some scrap may be mixed in as well. Similarly, while secondary steel is predominantly made using recycled steel scrap, some new iron may be used depending on the particular grade of steel or scrap availability.
-
Primary steel can be decarbonized by upgrading to new technologies powered by renewable energy, instead of fossil fuels, for the iron and steel processing steps.
• For ironmaking, in which iron ore is chemically reduced to metallic iron, one such technology is known as the direct reduction of iron (DRI). This method for producing iron substitutes natural gas and/or hydrogen for coke (processed coal) as the chemical reducing agent. Hydrogen produced from water electrolysis powered by renewables, also known as “green hydrogen,” is the most environmentally friendly form.
• For steelmaking, primary steelmakers can invest in electric arc furnaces, powered by 100% renewable energy, to produce the necessary steel while eliminating the majority of emissions.
When green hydrogen is used as the reducing agent in, the primary emission associated with ironmaking is water vapor, as opposed to carbon dioxide. Thus, by eliminating the need for coal, steelmakers can slash their customer’s supply chain emissions, while improving local air quality.
Find more about the basics of decarbonizing primary steel here.
-
Secondary steel can be decarbonized by repowering electric arc furnaces with 100% renewable electricity and sourcing low-carbon direct reduced iron for any non-scrap inputs.
-
Nearly one-third (30%) of the U.S. steel market is primary steel, produced by steelmakers such as Cleveland-Cliffs and U.S. Steel. The remaining 70% of steel produced in the U.S. is secondary.
Industries like automaking are currently heavily reliant on primary steel production. About 75% of the steel used in automobiles today is primary steel.
Due to the emissions intensity of primary steelmaking, a small number of blast furnaces, located at just a handful of steelmaking facilities in the Midwest, are responsible for nearly three-quarters (73%) of the U.S. steel industry’s annual emissions.
-
First, automakers today depend on primary steel because it is reliable for meeting the safety needs of high-strength components in vehicles, such as the body and frame components that provide stability and protect the passengers, while opting for secondary steel for components without industry-specified high-strength requirements. Second, even if secondary steel becomes a feasible choice for high-strength components, there’s not enough recycled steel today to meet the growing demands of the auto industry and other major purchasers of steel globally, let alone the entire clean energy economy.
For these reasons, the auto industry will continue to rely on primary steel for the foreseeable future.
-
An Environmental Product Declaration (EPD) is a standardized environmental claim from a manufacturer that provides transparent, audited information about a product’s environmental impact throughout its life cycle. EPDs act as a nutrition label for different steel products, allowing automakers to shop with confidence and make apples-to-apples comparisons of the carbon footprints (ton of CO2e per ton of steel) of each product.
-
EPDs are a useful tool for automakers to assess the emissions impact of the individual goods such as steel that they purchase from their supply chain in their vehicle manufacturing. Automakers can use EPDs to compare individual products such as primary steel from different producers or take a collective look at the emissions coming from their supply chain materials.
-
ResponsibleSteel™ is a certification created by an independent third party to verify the impact of steel products based on emissions and other environmental, social, and governance (ESG)-related factors such as pollution, responsible sourcing, human rights, labor standards, and more. ResponsibleSteel™ relies on a multi-stakeholder collaboration between business and civil society organizations and already has a number of participants, including U.S. Steel, ArcelorMittal, Boston Metal, and more. To be certified, steelmakers must have one site transformed to meet ResponsibleSteel™’s standards within one year of joining. Both primary and secondary steel can be certified as ResponsibleSteel™ to varying levels of emissions “from a basic threshold for ResponsibleSteel certification (level 1) through to the production of ‘near zero’ steel (level 4).”
ResponsibleSteel™ is an independent not-for-profit organization unaffiliated with Race To Green Steel.
-
No. While ResponsibleSteel™ certification is a great way to ensure that steel products meet minimum climate and ESG standards, any audited evaluation of multi-scope greenhouse gas emissions can be used to establish the climate impact of a steel product.
-
According to the EPA, “Carbon dioxide equivalent or CO2e means the number of metric tons of CO2 emissions with the same global warming potential as one metric ton of another greenhouse gas.”
Note: The language around prices used on this website is referring to $USD.
Ready to Join The Race?
If you’re ready to join the race to green steel, sign up for our newsletter and learn about how to get started, upcoming events and webinars, and more.